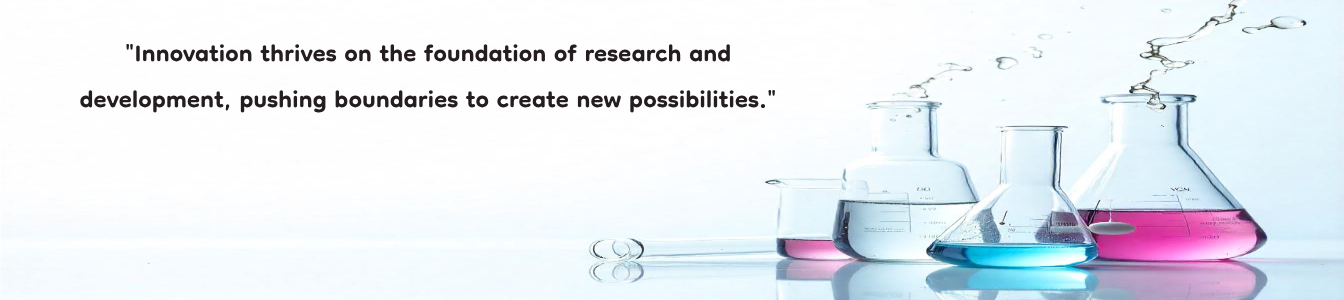
Our Products
ACTIVE NICKEL CATALYST
SPECIFICATIONS
Product | Activated Nickel Catalyst (Ready to use) |
Appearance | Metallic grey black, suspended in DM water |
Characteristic | Fine particles, highly pyrophoric in dry conditions |
Settled Density | 0.50-0.65 Kg Ni/Kg suspension |
Particle Size | Ranges from less than 32µ to maximum 160µ (From 100 mesh to around 400 mesh) |
Nickel Content | Greater than 88% |
Residual Aluminium | Not more than 12% |
Metal promoters (if any) |
1-3% |
pH Value | 8-10.5 |
Hydrogenation Activity | 25-90 ml H2/min (Nitrobenzene) |
About Active Nickel Catalyst
Active Nickel is a specialized form of finely divided, porous nickel catalyst prepared by selective leaching of aluminum from a nickel-aluminum alloy under carefully controlled conditions. This process involves treating powdered nickel-aluminum alloy with concentrated caustic soda, resulting in a slurry of spongy nickel particles. These particles are meticulously washed with large amounts of water until nearly free of residual caustic. Due to its pyrophoric nature, Active Nickel is highly flammable when dry and must be stored under water or a suitable solvent such as ethanol, cyclohexane, or dioxane. Commercial transactions, however, are typically conducted on a dry weight basis. Active Nickel is unsuitable for acidic environments below a pH of 5.5, as the nickel particles can dissolve, leading to a reduction in catalytic activity.
Uses and Applications
Active Nickel, with its unique spongy and highly reactive structure, serves as a powerful and versatile catalyst in hydrogenation reactions. It facilitates the hydrogenation of a wide range of functional groups, including carbon-carbon double bonds, carbonyl (aldehyde and ketone) groups, nitro, azide, nitrile, and oxime groups. Its applications span numerous industries such as food processing, pharmaceuticals, aromatics, petrochemicals, rubber additives, dye intermediates, drug intermediates, pesticides, caprolactam production, fine organic chemicals, and reactions involving hydrogenolysis (such as dehalogenation and debenzylation) and desulfurization. This catalyst is effective in both batch and continuous hydrogenation processes and can operate under extreme pressures and temperatures. Active Nickel is considered a non-specific catalyst due to its ability to hydrogenate nearly any reducible functional group in a molecule, often in varying degrees.
Distinct from most hydrogenation catalysts, Active Nickel has resistance to sulfur poisoning. Although it reacts readily with sulfur compounds due to nickel’s strong affinity for sulfur, this trait makes it especially suitable for desulfurization and dehydrogenation reactions.
Advantages of Active Nickel Catalyst
- Activated and Ready-to-Use: Pre-activated for immediate application in reactions.
- Improved Filtration: Its high-density properties promote accelerated settling, enhancing ease of filtration.
- Broad Range of Hydrogenation: Suitable for a diverse range of hydrogenation applications.
- Large Surface Area: Porous skeletal structure imparts high catalytic activity.
- Economic Alternative: Provides a cost-effective substitute for precious metal catalysts.
- Resistant to Poisoning and Sintering: Enhanced resistance against catalyst degradation.
Grades of Active Nickel Catalyst
Matik Industries provides a versatile range of active nickel catalysts, customized to fulfill diverse customer requirements. Alongside standard offerings, Matik Industries can create specialized variants featuring low activity levels, reduced pyrophoricity, neutral pH, and adjustable slurry densities. These catalysts are engineered for specialized applications, including carbazole synthesis, desulfurization, and formulations enhanced with molybdenum or chromium. Each catalyst is crafted for optimal filtration ease and is designed to withstand minor oxidant exposure, ensuring robust performance across applications.
Commitment to Quality
Matik Industries is committed to delivering high-quality Active Nickel catalysts. Our Quality Management System ensures strict adherence to standard operating procedures, ensuring consistency and excellence in every batch produced. Through ongoing research and development, we continuously improve our products to meet the evolving needs of our customers, offering bespoke solutions and optimized production processes for enhanced performance and reliability.